Business
We are happy to respond to your requests for civil engineering, agriculture, logistics, containers and functional industrial fabrics
We hold discussions with our customers to determine where and how they would like to use the product. Our product line is divided into civil engineering, agriculture, containers, logistics materials, and industrial fabrics, and we offer products and standards that best suit your needs from our wide range of product ideas. We can also provide items that are not in our product lineup from our own procurement network.
We create products that provide value to society
We have developed original blow molding, injection molding, and weaving technologies and constantly update our equipment to manufacture products that support a variety of sites. Each of our employees will also learn and improve to create products that meet the changing needs of society.
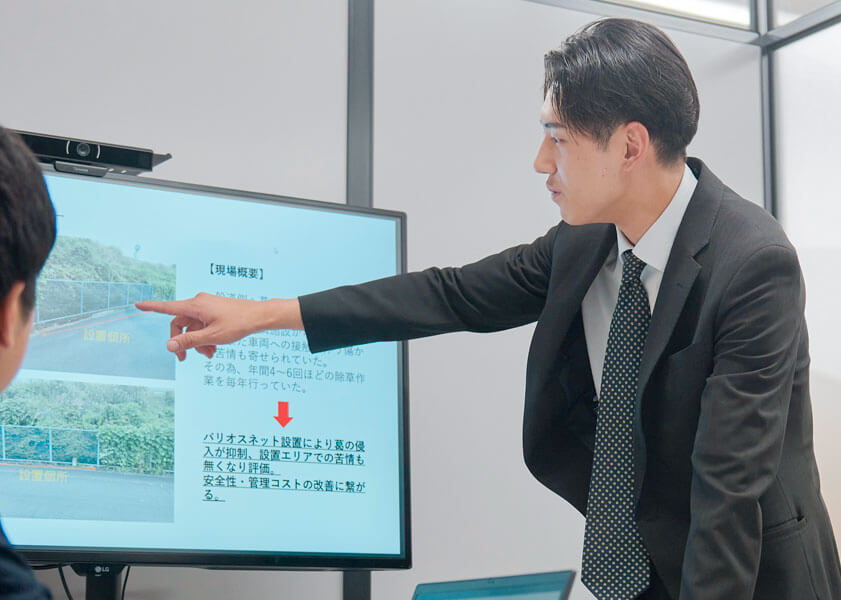
Shiga Plant
Technologies for Blow and Injection molding
We, KOIZUMISEIMA, started the blow molding business in 1982. Currently, the Shiga Plant, which serves as a manufacturing base for containers, produces blow-molded plastic containers and injection-molded for spouts and caps.

Blow molding
In blow molding, multiple plastic resins are melted as pellets and extruded into a parison shape by a molding machine, and containers are formed by blowing air into them to mold the resin to the shape of the mold. At the Shiga Plant, we can produce the "single layer blow molding type" with a single resin layer and the "multi-layer blow molding type" with multiple resin layers. The multi-layer blow molding type is superior in preserving the quality of the liquid content (long life), preventing oxidation and retaining aromas.
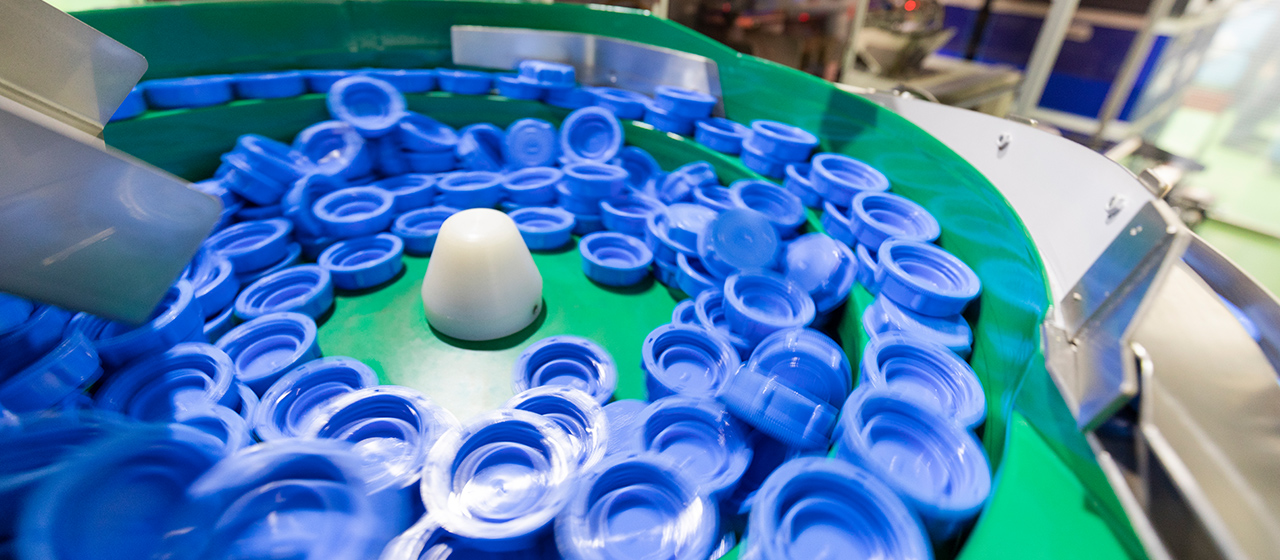
Injection molding
At the Shiga Plant, we process and produce injection molding products used in-house, such as caps and spouts (container mouth parts) for bag-in-boxes. The injection molding plant operates 24 hours a day, with nighttime production operating unmanned.
Quality control
At the Shiga Plant, we are working to build up product quality, strengthen hygiene management in the plant, and reduce environmental impact, and we have obtained three ISO certifications including the Quality Management System Certification (ISO 9001), Environmental Management System Certification (ISO 14001) and the Food Safety Management System Certification (ISO 22000).
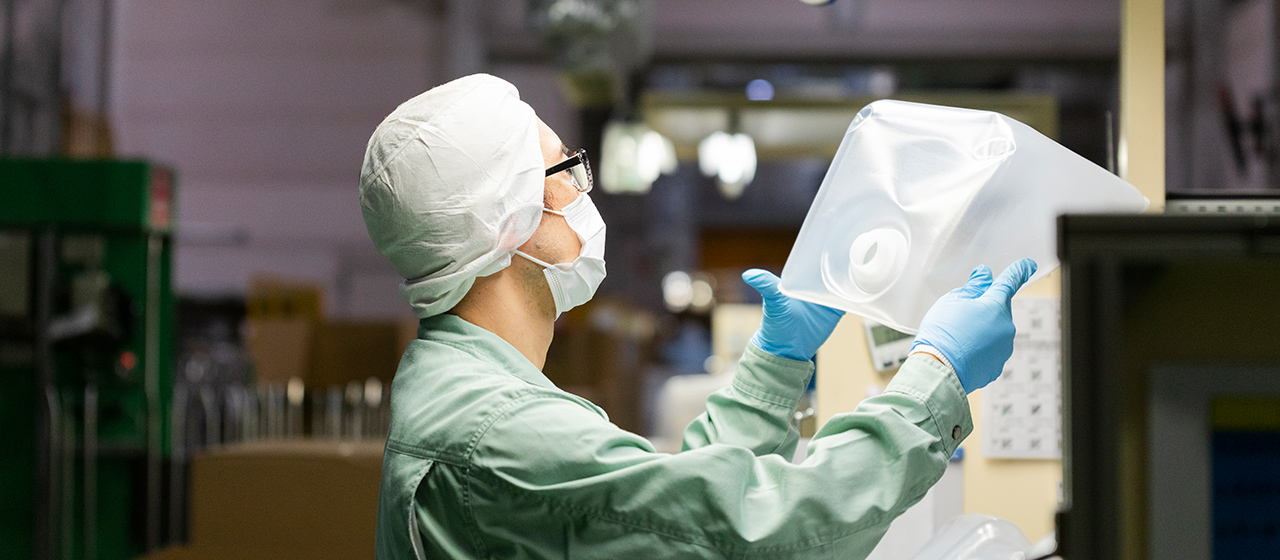
Hygiene control for use in food applications
The containers we produce are used for a variety of purposes, but in recent years they have been widely used for food products. In the future, we plan to produce BIB containers made of film in a plant with a higher level of cleanliness, and are working to meet the high hygiene control requirements of our customers.
Quality control to ensure safe use
The blow molding plant at the Shiga Plant has about 30 robots in operation, and once raw materials are fed in, production is unmanned until the containers are completed. All production lines are subjected to leakage inspection (pinhole inspection) to prevent liquid leakage, and quality is controlled at a high level.
Each employee will consider and attempt to improve
We have been actively engaged in 5S activities and improvement activities divided into small groups as an initiative for the entire plant since 2021. Each and every person working at the factory thinks and tries to ensure a stable supply of products that can be used with peace of mind. We are also expanding our testing facilities and manufacturing lines, and are working to develop products and manufacturing processes with lower environmental impact as a future challenge.
Kishiwada Plant
Yarn-making technology / weaving technology
Since the 1960s, we have been producing hemp fabrics, and now we produce a wide range of products including shading sheets, various weed prevention sheets, FIBC raw fabrics, and base fabrics for artificial turf, which are used for agricultural, logistics and civil engineering fields. We are implementing manufacturing of yarn called flat yarn to weaving process according to use application and function in a consistent manner. Especially the weed control sheet manufactured at Kishiwada Plant is manufactured by thinner yarn compared to that of competitors' products and the high-density woven fabric is created by using a lot of warp yarns in the weaving process to get a favorable reception after high weed control effect.
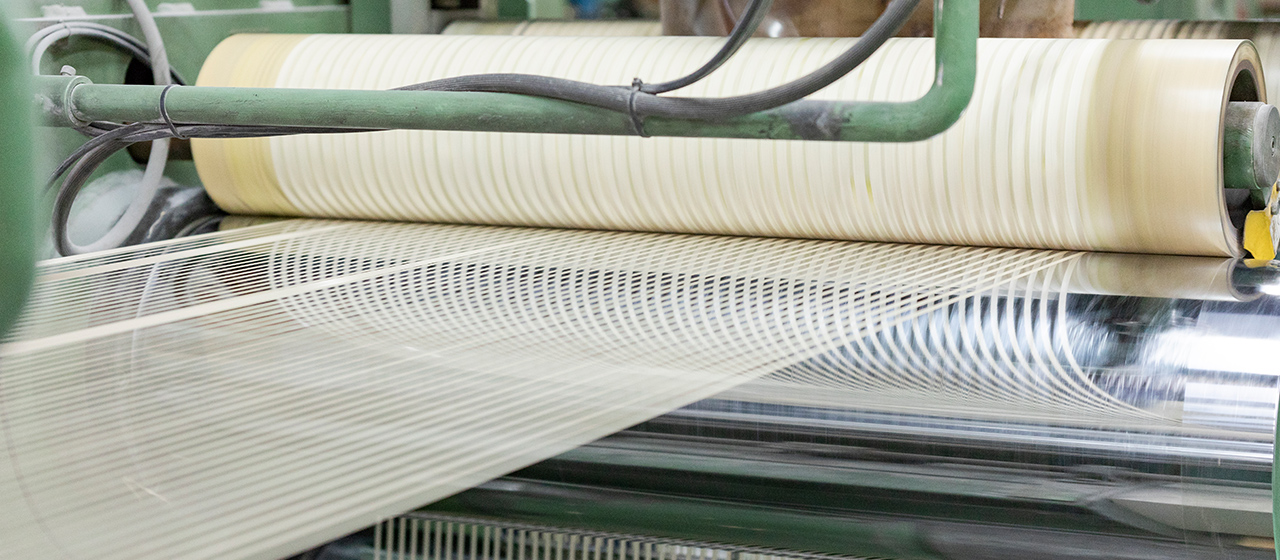
Production of flat yarn
A pellet type material is melted down and ejected in film shape, and then it is slit and expanded to manufactured the flat yarn. In addition, there is for blending raw materials with additives to produce yarns and it can be manufactured according to use application and function. The high reflectiveness of KOIZUMISEIMA's "RunRun Sheet Shiropika" is enabled by planning at the phase of yarn manufacturing.
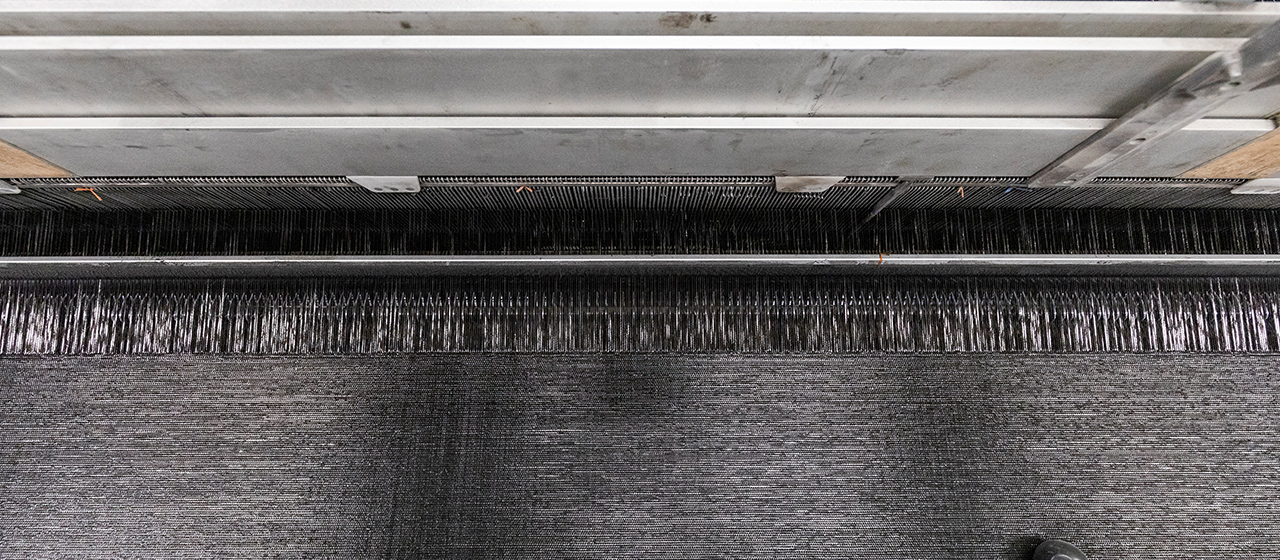
Weaving
What is manufactured at Kishiwada plant is “woven fabric”. In the weaving process, tension is controlled while inserting weft yarns into warp yarns, and films can be interwoven in addition to yarns to produce woven fabrics. By using highly functional films, we can create highly functional textile products.
Quality control
Kishiwada Plant has obtained the Quality Management System Certification (ISO9001) to provide products that gain the confidence and the satisfaction of customers.
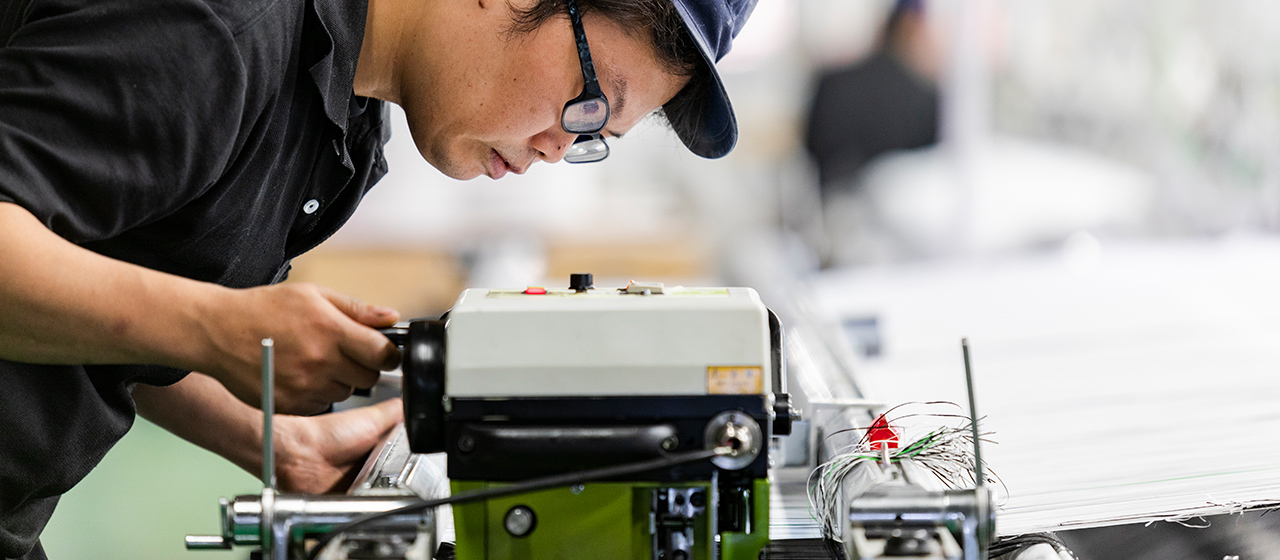
Manufacturing management by machine and human
Flat yarns are manufactured according to each determined process standards level, and are sent to the weaving process after the warp preparation process. The physical properties of the manufactured woven fabric are managed by human using various latest measuring instruments, and then it get approval for shipment for the last time.
Seeking the woven fabric in a new combination
We are seeking hybrid woven fabric with texture and functionality of natural fiber by interlacing hemp yarn and chemical yarn and addition of functionality in a special weaving method.